Conventional NDT
Comprehensive Conventional NDT Services
At ADVCCO, we are dedicated to providing high-quality Conventional Nondestructive Testing (NDT) services, ensuring the safety, reliability, and operational efficiency of your assets. With a blend of cutting-edge technology, industry expertise, and commitment to excellence, we deliver solutions that meet stringent safety standards and client expectations.
What is NDT?
Nondestructive Testing (NDT) is a critical inspection method used to evaluate the properties of materials, components, or assemblies without causing damage. These testing methods are fundamental to quality control, ensuring that assets meet operational and safety requirements. NDE methods have been trusted across industries for decades due to their proven effectiveness and versatility.
Key Features of Our NDT Services
Highly Skilled Inspectors: All our NDT technicians are certified to international standards such as ASNT, CSWIP, and PCN.
Cutting-Edge Technology: We leverage state-of-the-art equipment to ensure precise and reliable results.
Compliance with Standards: Our services adhere to industry codes, including ASME, API, ASTM, ISO, and EN.
Custom Inspection Plans: Tailored solutions to meet your specific project needs.
24/7 Availability: We provide round-the-clock support to minimize downtime and keep your operations running smoothly.
Our Conventional NDT Capabilities:
Our certified and highly skilled professionals are equipped to perform and execute the following NDE techniques:
- Ultrasonic Testing (UT)
- Phased Array Ultrasonic Testing (PAUT)
- Pulsed Eddy Current Testing (PECT)
- Magnetic Particle Testing (MPT)
- Radiographic Testing (RT)
- Penetrant Testing (PT)
- Visual Testing (VT)
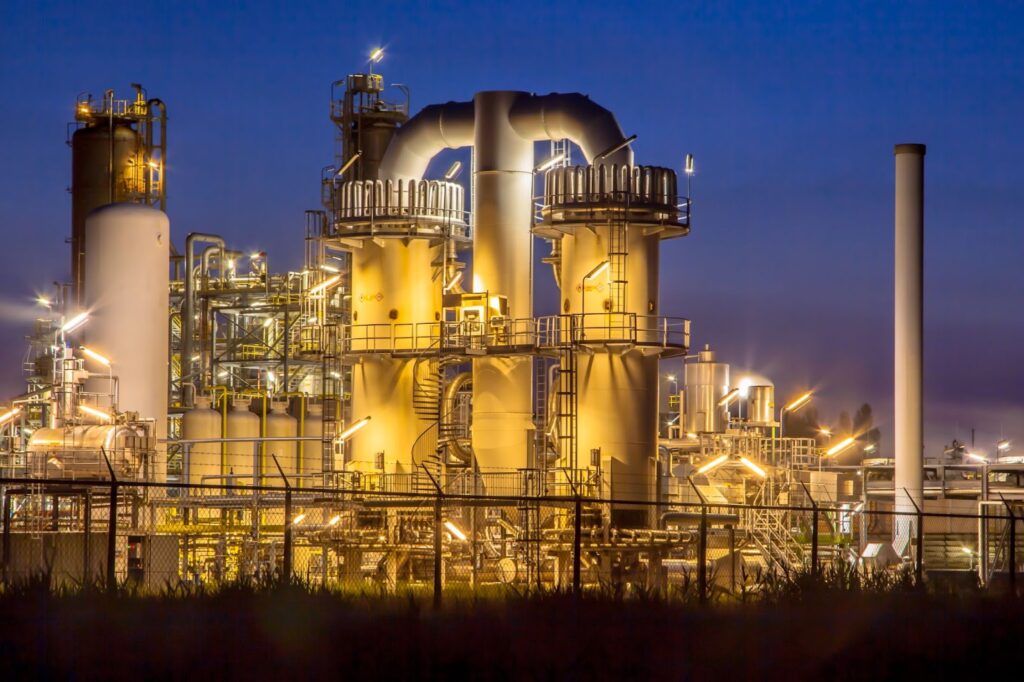
Industries We Serve
We proudly support a wide range of industries, including:- Oil & Gas: Inspection of pipelines, storage tanks, and refinery equipment.
- Power Generation: Assessment of boilers, turbines, and heat exchangers.
- Petrochemical: Quality assurance for critical components in processing plants.
- Manufacturing: Ensuring defect-free production of parts and assemblies.
- Construction: Inspection of structural welds and reinforcement components.
Ultrasonic Testing (UT):
Description: Ultrasonic waves are introduced into a material, and the reflected signals are analyzed to detect internal flaws.
Applications:
- Weld inspections for porosity, cracks, and inclusions.
- Thickness measurements to monitor corrosion and erosion.
- Flaw detection in forgings and castings.
Benefits: High accuracy, real-time results, and the ability to detect deep-seated defects.
Phased Array Ultrasonic Testing (PAUT):
Description: An advanced form of ultrasonic testing that uses multiple ultrasonic beams to create detailed cross-sectional images of a material or weld.
Applications:
- Inspection of complex geometries, such as nozzles and welds.
- High-resolution imaging for critical components in pipelines, pressure vessels, and aerospace structures.
Benefits: Precise defect characterization, enhanced coverage, and reduced inspection time compared to conventional UT.
Pulsed Eddy Current Testing (PECT):
Description: A non-contact electromagnetic testing method that uses pulsed eddy currents to detect corrosion and wall loss in components, especially under insulation.
Applications:
- Corrosion Under Insulation (CUI) inspections in pipelines, tanks, and vessels.
- Thickness measurements in inaccessible or insulated areas.
Benefits: No need to remove insulation, quick scanning of large areas, and effective for evaluating wall loss in ferrous materials.
Magnetic Particle Testing (MPT):
Description: A magnetic field is applied to ferromagnetic materials, and iron particles are used to highlight surface and near-surface discontinuities.
Applications:
- Inspection of pipelines, shafts, and machine components.
- Detection of fatigue cracks, seams, and inclusions.
Benefits: Quick and reliable results with minimal preparation required.
Radiographic Testing (RT):
Description: X-rays or gamma rays penetrate a material to produce an image, highlighting internal defects.
Applications:
- Weld quality verification in pipelines and structural components.
- Inspection of castings for porosity and shrinkage.
Benefits: Permanent record of inspection and the ability to inspect hidden areas.
Liquid Penetrant Testing (PT):
Description: A penetrant is applied to the material’s surface, followed by the use of a developer to make surface-breaking flaws visible.
Applications:
- Inspection of non-porous materials such as metals, ceramics, and plastics.
- Detection of cracks, laps, and leaks in components.
Benefits: Easy to apply, low cost, and highly effective for surface inspections
Visual Testing (VT):
Description: Direct or remote inspection of a component’s surface to identify defects.
Applications:
- Quality control in manufacturing.
- Pre-weld and post-weld inspections.
Benefits: Fast, cost-effective, and non-invasive.
Why Choose Us?
Experience You Can Trust: Decades of expertise in the field of NDT ensure reliable outcomes.
Precision and Accuracy: Advanced equipment and skilled inspectors guarantee high-quality results.
Commitment to Safety: We prioritize the safety of your assets and personnel through rigorous inspections.
Cost-Effective Solutions: Our efficient services reduce operational risks and prevent costly failures.
Sustainability: By identifying issues early, we help extend the lifecycle of your assets and minimize waste.